Key Tronic Corporation (NASDAQ:KTCC) Q4 2023 Earnings Call Transcript August 18, 2023
Operator: Good day, and welcome to the fiscal 2023 Fourth Quarter and Year-End Key Tronic Corporation Conference Call. Today’s conference is being recorded. At this time, I would like to turn the conference over to Brett Larsen. Please go ahead.
Brett Larsen: Thank you. Good afternoon, everyone. I am Brett Larsen, Chief Financial Officer of Key Tronic. I would like to thank everyone for joining us today for our investor conference call. Joining me here in our Spokane Valley headquarters is Craig Gates, our President and Chief Executive Officer. As always, I would like to remind you that during the course of this call, we might make projections or other forward-looking statements regarding future events or the company’s future financial performance. Please remember that such statements are only predictions. Actual events or results may differ materially. For more information, you may review the risk factors outlined in the documents the company has filed with the SEC, specifically our latest 10-K, quarterly 10-Qs and 8-Ks. Please note that on this call, we will discuss historical financial and other statistical information regarding our business and operations.
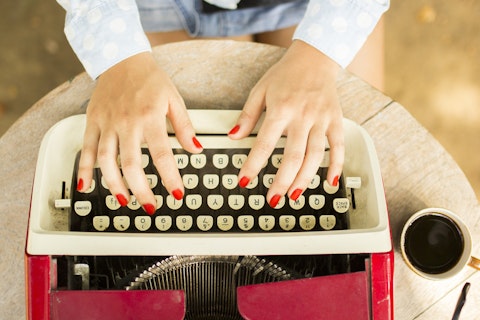
Who is Danny/Shutterstock.com
Some of this information is included in today’s press release and a recorded version of this call will be available on our website. Today, we released our results for the quarter and year ended July 1, 2023. For the fourth quarter of fiscal 2023, we reported total revenue of $162.6 million, up 29% from $126.2 million in the same period of fiscal year 2022. For the full year of fiscal 2023, total revenue was $588.1 million, a company record and up 11% from $531.8 million for the fiscal year of 2022. Revenue for the fiscal year 2023 included new program ramps as well as increased demand from a number of long-standing customer programs. For the fourth quarter of fiscal 2023, our gross margin was 8.5% and operating margin was 2.6% compared to gross margin of 9.3% and an operating margin of 1.8% in the same period of fiscal year 2022.
Our gross margin in the fourth quarter of fiscal year 2023 continued to be adversely impacted by the strengthening of the Mexican peso relative to the US dollar. Roughly over $20 million of production costs are denominated in Mexican peso that were impacted. At the same time, we continue to see improvements in our production efficiencies, implemented strategic labor cost reductions, and have seen a gradual stabilization in the supply chain and labor markets. For the fourth quarter of fiscal 2023, our net income was $1.1 million or $0.10 per share, up from $1 million or $0.09 per share for the same period of fiscal year 2022. For the full year of fiscal 2023, net income was $5.2 million or $0.47 per share, up 53% from $3.4 million or $0.31 per share for the fiscal year 2022.
Turning to the balance sheet. We ended the fourth quarter of fiscal 2023 with total working capital of $198.3 million and a current ratio of 2.3:1. Our receivables increased by $15.8 million from a year ago, reflecting the growth in our revenue levels. At the same time, our DSOs were at 82.5 days, down from 92.5 days a year ago, which we believe reflects some improvement of certain customers with respect to disruptions from COVID-19 and other supply chain issues. At the end of fourth quarter of fiscal 2023, our inventory decreased by approximately $16.8 million or by 11% from the same time a year ago, primarily reflecting increased shipments and a concerted effort to drive inventory reductions. Our inventory turns increased to 3.7 times in the fourth quarter of fiscal year 2023, up from 2.9 times a year ago.
While the state of the worldwide supply chain still requires that we look out much further in the future than in historical periods, we attempt to carefully balance customer demand and the likelihood of successfully bringing in parts in time for planned production. In coming quarters, we expect to see our inventory levels continue to decrease at a slower rate, in line with revenue levels. Total capital expenditures were about $400,000 for the fourth quarter of fiscal 2023 and total CapEx for the year was $5.3 million. During the year, we also utilized the insurance proceeds from storm damage to modernize our operations, which should increase efficiencies in our Arkansas facility. While we’re keeping a careful eye on capital expenditures, we plan to continue to invest selectively in our production equipment, SMT equipment and plastic molding capabilities, utilized leasing facilities as well as make efficiency improvements to prepare for growth and add capacity.
We move into fiscal 2024 with a strong backlog and a pipeline of potential new business, our inventory more in line with our revenue levels, and we’re continuing to see improvement in the global supply issues and lower labor turnover. On the other hand, we’re seeing some softening in demand from several large customer, and one large customer is pausing production in this first quarter to resolve certain of their design issues. We also expect the stronger Mexican peso and our relatively high interest expense to constrain our bottom line. For the first quarter of fiscal 2024, we expect to report revenue in the range of $135 million to $145 million and earnings in the range of $0.05 to $0.10 per diluted share. Over the longer term, however, we believe that we are increasingly well positioned to win new EMS programs and continually and profitably expand our business.
That’s it for me. Craig?
Craig Gates: Okay. Thanks, Brett. Fiscal 2023 was a record-breaking year for Key Tronic. We’re pleased with our record annual revenue and strong earnings, driven by our successful ramp of new programs. As Brett noted, revenue grew 11% and earnings grew 53% from the prior year, despite facing many ongoing challenges with the supply chains and labor markets and despite higher interest expense and foreign currency pressures. During the year, we continued to see the favorable trend of contract manufacturing returning to North America. As a result, we continue to expand our customer base and won new programs involving a wide range of industries. Outdoor power equipment, battery management, automated sprinklers, biometric sensors, audio technology, automation, electric vehicles, power distribution, security devices, video and pinball machines, mining, safety and productivity, telecommunications, inventory control, clean energy, and distribution monitoring equipment.
Mobile logistics problems, the war in Europe and China-US geopolitical tensions continue to drive OEMs to examine their traditional outsourcing strategies. We believe these customers increasingly realize that they have become overly dependent on their China-based contract manufacturers for not only product but also for design and logistics services. Over time, the decision to onshore or nearshore production is becoming more widely accepted as a smart long-term strategy. As a result, we see opportunities for continued growth. As we’ve discussed in prior calls, we built Key Tronic to offer the ideal solution for customers as they move to respond to geopolitical pressures. Our facilities in Mexico represent a campus of 1.1 million square feet in Juarez, most of which is contiguously located in nine facilities acquired over time.
Our 3 US-based manufacturing sites have also benefited greatly from the macro forces driving business back to North America. Moreover, a growing number of political customers or political potential customers are actively evaluating a migration of their China-based manufacturing to our facility in Vietnam. In the coming years, we expect our Vietnam facility to play a major role in our growth. Our Shanghai plant has added capabilities in management, staff and systems that allow to serve Chinese customers directly. Shanghai has replaced the business that we moved to Vietnam, and while China growth has slowed and many companies have decided to take risk mitigation steps with their China manufacturers, the fact remains that many components must be sourced from China.
Our procurement group in Shanghai, which serves the entire corporation, is important for managing the China component supply chain on an ongoing basis. The combination of our global footprint and our expansive design capabilities is proving to be extremely effective in capturing new business. Many of our large and medium-sized manufacturing program wins are predicated on Key Tronic’s deep and broad design services. And once we have completed the design and ramped it into production, we believe our knowledge of a program-specific design challenges makes that business extremely sticky. We also invested in vertical integration and manufacturing process knowledge, including a wide range of plastic molding, injection, blow, gas-assist multi-shot as well as PCB assembly, metal forming, painting and coding, complex high-volume automated assembly and the design, construction and operation of complicated test equipment.
This expertise may set us apart from our competitors of a similar size. As a result, a customer looking to leave their contract manufacturer will find a one-stop shop in Key Tronic, which is expected to make the transition to our facilities much less risky and cobbling together a group of providers each limited to a portion of the value chain. We believe global logistics problems, China-US political tensions and heightened concerns about supply chains will continue to drive the favorable trend of contract manufacturing returning to North America as well as to our expanded Vietnamese facilities. Along with the records we set for revenue and strong earnings in fiscal 2023, we continue to see improvement across the metrics associated with business development, including a significant increase in number of active quotes with respective customers.
This unprecedented increase in demand for our unique mix of skills, location, people has powerful implications beyond the obvious revenue growth potential. In particular, we have been able to negotiate more favorable pricing terms and business parameters than in the past as well as to be much more selective in the new customers we bring on. While this shift in leverage will not manifest itself in the short term, its effect on our long-term performance should be profound. We move into fiscal 2024 with a strong pipeline of potential new business, and we’re seeing improvement in the global supply issues and lower labor turnover, which severely limited our production in prior periods. While we see some production delays and softness in demand in Q1 and we can expect higher interest rates and a strong peso to dampen our profitability in the near term, we’re very encouraged by our progress and potential for growth in fiscal 2024 and beyond.
In closing, I want to emphasize that the execution of our strategy was made possible not only by our investments in plants and equipment, but even more so the skills, local knowledge and talents of our people. I want to thank our exceptional employees for their dedication and hard work during this past year and our shareholders for their continued support. This continues — this concludes the formal portion of our presentation. Brett and I will now be pleased to answer your questions.
See also 10 Dividend Stocks with Over 8% Yield and 20 Most Dangerous Countries in Africa.
Q&A Session
Follow Key Tronic Corp (NASDAQ:KTCC)
Follow Key Tronic Corp (NASDAQ:KTCC)
Operator: [Operator Instructions] And our first question comes from Bill Dezellem with Tieton Capital. Your line is open.
Bill Dezellem: Thank you. Would you please walk through the size of each of the new wins this quarter?
Craig Gates: Yeah, it was a little bit over 10, close to five and close to three.
Bill Dezellem: Great. Thank you. And then relative to the design issue that you’re seeing with the customer, what is the size of the revenue impact that’s anticipated here in the third quarter — pardon me, in the third calendar quarter, your first fiscal quarter?
Craig Gates: We’re not quite sure yet depending on when we restart.
Bill Dezellem: Would a fair way to look at that be to just ask what was their revenue level either in Q4 or Q1 a year ago?
Craig Gates: Probably a fair way to look at it is to say that the numbers we’re projecting have zero for that product in Q1.
Bill Dezellem: And so what was — what was the number a year ago or in Q4?
Craig Gates: Number a year ago was also zero. And Q4, I guess I can’t tell you that number.
Bill Dezellem: And then, let’s actually circle back to Q4. You had a customer that was seasonally slowed or ended their production in Q4 that had been pretty significant in Q3. When will they be starting back up? And do we anticipate some revenue in Q1 from now?
Craig Gates: That revenue is zeroed out in Q1 in the projection we gave you.
Bill Dezellem: Okay. Great. Lastly, relative to Vietnam, you made a couple of positive comments in the opening remarks. Could you kind of provide a more in-depth update, what you’re seeing with Vietnam, please?
Craig Gates: We are seeing quite a few people stop by and visit now in preparation for making a decision. That shutdown entirely for almost two years during COVID, and now that’s ramping back up again. We’re seeing Vietnam is more and more in fashion for our procurement folks of our customers to think about. So we expect a bright future there. We have land nearby to grow. So we expect that we won’t have a problem expanding our facilities, and we do not see as of yet [denying] (ph) being overwhelmed with business. So everything looks pretty good so far.
Bill Dezellem: And how much business do you currently have in the Vietnam facility? And what is your approximate capacity, or said another way, kind of roughly when, what you see today might you need to expand that plant?
Craig Gates: About 30 there now, and we can probably double that, maybe a little bit more before we need to expand the plant. It always depends on if it’s just pure PCB or if it’s box build or somewhere in between.
Bill Dezellem: Right. Great. Thank you, Craig.
Operator: [Operator Instructions] And our next question comes from the line of George Melas with MKH Management. Please go ahead.
George Melas: Hey, good afternoon, guys.
Brett Larsen: Hi, George.
George Melas: Hey, Brett. I’m just trying to put numbers to the impact of the increased valuation of the peso versus the dollar. And I sort of see that year-over-year, the peso growing roughly 18% versus the dollar. And so — and tell me if I have it sort of directionally right. If your labor costs are roughly $20 million, then that’s sort of an increase of $2.5 million to $5 million. Is that roughly right?
Brett Larsen: Yeah, that is correct. And that $20 million we disclosed is actually not just labor, but it’s all our Mexican peso costs, which would, of course, include some lease and utilities and those types of things that are paid down in Mexico. But yes, directionally, you are correct.
George Melas: And do you have sort of a provision in your contracts to try to be able to pass that to the customer or is it just one of your arguments in sort of some kind of annual contract negotiation?
Craig Gates: George, the answer to that is yes and yes. So most of the contracts have a provision in there that allows us to increase our prices when we see this type of increased costs. But none of those provisions ever get tripped automatically when it results in a customer being forced to pay a higher price. So it always results in a discussion about what’s actually going to happen.
George Melas: Okay. So just to understand that you have a clause in the contract but you still need to bring it up to the customer. It’s not automatic. You need to bring it up to the customer and agree on some kind of increase.